PROJECTILE GUIDES
Introduction
The projectile guide employs support teeth which have horizontal disposed support surfaces for slid ably receiving and supporting a picked projectile thereon. In addition, alternately arranged guide teeth are provided to define a picking tunnel while also providing a lateral guide on one side of the horizontal support surfaces to prevent sliding off a projectile threat. A lateral guide surface may also be provide on the support teeth on one side of the support surface to prevent lateral movement from an opposite side of the support surface.
The limited weight and the reduced volume of the projectile make a projectile guide necessary (fig: 1 ). The projectiles therefore do not come into contact with the threads, but run inside a sort of channel composed of the thin prongs of a rake, which form reminds a semi closed hand. This rake goes up from under the threads at the moment of the projectile launch and has of course to fall back lowering itself at the slay stroke. To enable this movement, the rake is secured on the slay and is positioned very close to the reed; the rake’s laminas are not in contact with the warp, or touch it very lightly because the reed opens them the way. The latest models of the projectile machine have been equipped with new types of guide dents, which are divided and placed in alternate position, in order to reduce the stress on weft and warp threads. This permits to use in warp even very delicate yarns as for instance untwisted or entangled yarns and at the same time to cope with high quality requirements.
![]() |
Fig 1: Projectile and projectile guide in a weaving machine |
Projectile guide for a weaving machine
Heretofore, various types of guides have been known for use in a projectile weaving machine and particular weaving machine which employ gripper projectile. In some cases, the guides have been constructed of a plurality of guide teeth which are shaped to define a picking tunnel through which a picking element, such as a projectile, may be picked .Generally, the guide teeth have been formed with a plurals of surfaces for guiding of a projectile whereas in other cases ,an alternating arrangement of support teeth and guide teeth have been used to define the guide surface for the projectile. In addition the guide teeth have been constructed to provide an aperture on the reed side of the in order to permit release to of a picked weft yarn before the reed beats the yarn into a cloth.
![]() |
Fig 2: Projectile guide on sley. |
German Pat. No. 1,801,004 filed Oct. 4, 1968 describes a projectile guide which employs two bottom include guide surface and one top horizontal guide surface for guiding a projectile during picking through a shed. However, the inclined arrangement of the bottom guide surfaces leads to support forces which are considerable more than the weight of the projectile. For example, if these surfaces are inclined at an angle of 45 degrees to a horizontal , the sum of the support forces and in a first approximation , the sum of the friction forces is some 40% more than when the projectile is supported on a surface normal to the direction in which the weight acts. Further , when the sley on which the guide is mounted vibrates around the pivot point of the sley , the effect of the inclined guide surfaces is to throw the projectile from one bottom guide surface to the other and back with the projectile possibly striking the top horizontal guide because of the unsteady flight of the projectile with continuously changing impact positions on the guide surfaces and because of the associated friction forces , an elaborate lubrication system must be provided for an accurately metered supply of lubricant to the weft tunnel if wear of the tunnel is to be obviated.
![]() |
Fig 3: Illustrates a view in a picking direction of a previously known projectile guide. |
In another know projectile guide, as described in Swiss Pat. No. 439,159, closed guide projections have a guide surface which extends transversely to the forces associated with projectile weight. The forces with which such projectile reacts on the projectile are less in this case, so that the friction between the projectile and the guide is also less. However a disadvantage of this guide has been found to be that when the guide dips into the shed , with the guide teeth penetrating through the bottom warp plane with their opening at the front discrete warp yarns may penetrate into the interior of a guide projection. Thus, there is a risk that the warp yarns may be damaged or severed between the projectile and a guide projection. This risk is particularly great near the weaving edge where, because of the shrinkage or contraction of many woven fabrics, the warp yarns do not extend parallel to the guide projections.
Accordingly, it is an object of the invention to provide an improved projectile guide for a weaving machine.
It is another object of the invention to reduce the risk of warp yarn breakages by a projectile guide a weaving operation.
It is another object of the invention to reduce the wear in a projectile guide due to the sliding of a projectile there through.
Briefly, the invention provides a projectile guide for a weaving machine which is comprised of a plurality of longitudinally aligned and spaced apart support teeth and a plurality of guide teeth disposed in alternating relation with the support teeth. In accordance with the innovation, each support tooth has at least one horizontally disposed support surface for slid ably receiving and supporting a picking projectile thereom.In addition each guide tooth is provided with guide surfaces for preventing surface of the support teeth during picking.
The construction of the projectile guide is such that there is reduced friction between the projectile and the teeth of the guide. In addition there is less risk of a warp yarn catching inside of a guide or support tooth. Accordingly, weaving can proceed with less coolant being supplied to a weft tunnel defined by the support teeth and guide teeth and with fewer stoppages due to damage of the warp.
In one embodiment, each support tooth includes an inclined surface defining a lateral guide on one side of the support surface in order to prevent lateral sliding of a picked projectile from the support surface. In addition each guide tooth has a guide surface defining a lateral guide on an opposite side of the support surface of an adjacent support tooth in order to prevent lateral sliding of a picked projectile threat. Further, each guide tooth has a horizontally disposed guide surface in a plane above the support surface of an adjacent support tooth in order to loom lifting of a picked projectile from the support surface of the adjacent tooth.
The guide surface of the projectile guide which act laterally or downwardly on a projectile are operative merely to defect the projectile into the required direction in the event the projectile deviates from a path dead parallel to the weft tunnel. In the cases of previously known projectile guides. The lateral guide surfaces serve to support the projectile. Consequently the clearance between the guide surfaces of the projectile guide and a projectile can be considerably greater than in previously known guides. When the projectile is guided dead parallel to the weft tunnel before entering the tunnel, the only contact between the guide surfaces and the projectile is by way of the horizontal support surface of a support tooth.
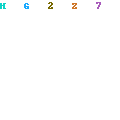